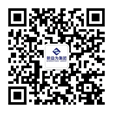
微信公眾號二維碼
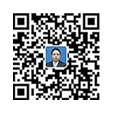
微信咨詢顧問二維碼
TPM咨詢重塑公司的設(shè)備管理體系?新益為TPM咨詢公司概述:在現(xiàn)代化制造現(xiàn)場,設(shè)備如同企業(yè)的骨骼與血脈。它們晝夜不停地運轉(zhuǎn),承載著產(chǎn)量、質(zhì)量與交付的核心使命。然而,現(xiàn)實往往充滿挑戰(zhàn):設(shè)備故障頻發(fā),產(chǎn)線意外停機成為常態(tài);維修成本居高不下,備件庫存堆積如山;設(shè)備效率遠未達設(shè)計水平,綜合效率OEE長期低迷;操作工只會使用,不懂保養(yǎng),維修人員疲于奔命;設(shè)備相關(guān)質(zhì)量波動難以根除,安全事故時有發(fā)生。這些看似孤立的問題,實則是企業(yè)成本失控、效率低下、競爭力削弱的深層癥結(jié),其根源往往在于設(shè)備管理體系的不完善與全員參與機制的缺失。
TPM咨詢
面對這些系統(tǒng)性的設(shè)備管理難題,傳統(tǒng)“頭痛醫(yī)頭、腳痛醫(yī)腳”的維修策略已力不從心。此時,系統(tǒng)化、全員參與的TPM咨詢(全員生產(chǎn)維護)的價值便如破局之鑰。TPM不僅僅是一種維修策略,更是一種追求設(shè)備綜合效率最大化、損失為零的企業(yè)經(jīng)營哲學(xué)。專業(yè)的TPM咨詢服務(wù),正是幫助企業(yè)導(dǎo)入這套先進理念和方法論,實現(xiàn)設(shè)備管理從被動響應(yīng)到主動預(yù)防、從局部改善到系統(tǒng)優(yōu)化的革命性轉(zhuǎn)變。它基于深入的企業(yè)診斷,精準識別設(shè)備管理在策略、流程、技術(shù)、人員技能及文化氛圍等維度的核心短板,為企業(yè)量身定制通向“零故障、零缺陷、零事故”目標的清晰路徑。
TPM的核心精髓在于“全員參與”。它徹底打破“操作只管用、維修只管修”的傳統(tǒng)壁壘,強調(diào)設(shè)備是生產(chǎn)的伙伴,其維護是全體人員的共同責(zé)任。TPM咨詢的首要任務(wù),便是重塑企業(yè)設(shè)備管理的文化基因與責(zé)任體系。通過系統(tǒng)的理念導(dǎo)入與宣貫,引導(dǎo)從高層管理者到一線操作工、維修技師,深刻理解TPM的八大支柱(自主維護、專業(yè)維護、個別改善、初期管理、質(zhì)量維護、安全環(huán)境、教育訓(xùn)練、間接效率)內(nèi)涵及其對企業(yè)的戰(zhàn)略價值。更為關(guān)鍵的是,TPM咨詢會協(xié)助企業(yè)建立清晰的角色職責(zé)劃分:操作工需掌握基礎(chǔ)的設(shè)備清掃、點檢、潤滑、緊固及微小故障處理技能(自主維護);維修人員則需聚焦預(yù)測性維護、計劃性檢修及技術(shù)難題攻關(guān)(專業(yè)維護);管理者需提供資源支持、設(shè)定目標、營造氛圍。這種責(zé)任共擔(dān)的文化重塑,是TPM成功落地的基石。
自主維護是TPM最具特色的支柱,也是釋放操作工潛能的關(guān)鍵。TPM咨詢將系統(tǒng)性地指導(dǎo)企業(yè)實施自主維護的七步法:從徹底的初期清掃開始,識別并消除污染源、困難源;通過點檢基準的制定與可視化,讓操作工掌握發(fā)現(xiàn)設(shè)備異常的能力;進行自主性的潤滑管理、緊固管理;最終形成標準化、可持續(xù)的自主維護流程。這個過程并非一蹴而就,TPM咨詢專家會深入現(xiàn)場,通過“手把手”的教練式輔導(dǎo),教導(dǎo)員工如何正確使用工具、識別微小缺陷、理解設(shè)備結(jié)構(gòu)原理(一點課OPL),逐步提升其設(shè)備保全能力與“主人翁”意識。當(dāng)操作工從設(shè)備的“使用者”轉(zhuǎn)變?yōu)?ldquo;守護者”,大量潛在故障在萌芽狀態(tài)即被消除,設(shè)備穩(wěn)定性將獲得質(zhì)的飛躍。
設(shè)備效率的持續(xù)提升,離不開對損失的系統(tǒng)性分析與消除。TPM咨詢的核心武器之一是聚焦設(shè)備六大損失(故障損失、換模換線損失、速度損失、空轉(zhuǎn)短暫停機損失、啟動損失、不良返工損失)的識別、測量與改善。借助專業(yè)的OEE(設(shè)備綜合效率)分析工具,TPM咨詢幫助企業(yè)建立精確的設(shè)備績效測量體系,暴露真實的效率瓶頸。在此基礎(chǔ)上,引導(dǎo)跨職能團隊(操作、維修、工藝、設(shè)備)運用精益工具和問題解決方法(如5Why分析、PM分析、FMEA、快速換模SMED),對關(guān)鍵損失進行根源性攻關(guān)。每一個改善項目的成功,不僅帶來可觀的效率提升和成本節(jié)約,更積累了團隊解決問題的信心與能力,營造出持續(xù)改善的強勁勢頭。
預(yù)防性維護體系的科學(xué)化與高效化,是減少突發(fā)故障、降低維修成本的核心。TPM咨詢將協(xié)助企業(yè)優(yōu)化維修策略組合:依據(jù)設(shè)備關(guān)鍵性和故障模式,科學(xué)分配事后維修、定期預(yù)防性維護、狀態(tài)監(jiān)測(預(yù)測性維護)的比例。重點提升預(yù)測性維護能力,指導(dǎo)企業(yè)引入適用的狀態(tài)監(jiān)測技術(shù)(如振動分析、油液分析、紅外熱成像),建立設(shè)備健康狀態(tài)預(yù)警機制。同時,TPM咨詢會幫助企業(yè)梳理并優(yōu)化維修工單流程、備件管理體系(包括合理庫存設(shè)定與采購策略)、維修技術(shù)標準(維修作業(yè)指導(dǎo)書),提升維修計劃性與執(zhí)行效率。在此基礎(chǔ)之上,推動維修部門向“專業(yè)維護”轉(zhuǎn)型,開展深度設(shè)備劣化分析、壽命周期成本管理(LCC)和維修技術(shù)攻關(guān),從根源上提升設(shè)備可靠性與維修經(jīng)濟性。
設(shè)備管理的卓越,始于良好的開端。TPM咨詢將TPM理念前伸至設(shè)備生命周期的源頭——規(guī)劃、選型與安裝調(diào)試階段(MP設(shè)計:維護預(yù)防)。它引導(dǎo)企業(yè)在設(shè)備前期管理中,就充分考慮后期的可維護性、可靠性、可操作性及安全性需求。TPM咨詢專家可參與設(shè)備技術(shù)規(guī)格書的評審,提出維護友好性設(shè)計建議(如易于點檢、潤滑、維修的布局,標準化接口,故障診斷功能);在新設(shè)備安裝調(diào)試階段(初期流動管理),協(xié)助建立完善的初期清掃、點檢基準,收集運行數(shù)據(jù),快速暴露并解決初期故障隱患,確保設(shè)備從投產(chǎn)伊始就處于最佳狀態(tài),避免“先天不足”帶來的長期困擾。
安全是生產(chǎn)的底線,質(zhì)量是企業(yè)的生命,而設(shè)備是保障安全與質(zhì)量的基石。TPM咨詢深諳此道,將安全與環(huán)境管理、質(zhì)量維護作為核心支柱貫穿始終。它幫助企業(yè)建立設(shè)備安全防護裝置的點檢與維護標準,消除設(shè)備安全隱患;通過提升設(shè)備精度和穩(wěn)定性,減少因設(shè)備原因?qū)е碌馁|(zhì)量波動(質(zhì)量維護),將質(zhì)量保證構(gòu)筑在設(shè)備管理之上。TPM咨詢的精髓在于構(gòu)建一個以設(shè)備為紐帶,集效率、質(zhì)量、安全、成本于一體的綜合管理體系,實現(xiàn)多維度價值的協(xié)同提升。
選擇專業(yè)的TPM咨詢服務(wù),是企業(yè)對核心制造能力的一次戰(zhàn)略性升級投資。其回報清晰可見:設(shè)備故障停機時間大幅下降(通??蛇_50%以上),OEE綜合效率顯著提升(提升10%-30%);維修成本及備件庫存得到有效控制;產(chǎn)品質(zhì)量更加穩(wěn)定,安全事故率顯著降低;員工技能提升,參與改善的熱情高漲。更為深遠的意義在于,它為企業(yè)構(gòu)建了一套基于全員參與、持續(xù)改善的設(shè)備精益管理體系和文化,鍛造了應(yīng)對市場變化、實現(xiàn)可持續(xù)發(fā)展的核心制造競爭力。在制造業(yè)轉(zhuǎn)型升級的關(guān)鍵時期,TPM咨詢正是企業(yè)激活設(shè)備潛能、邁向智能制造、贏得未來競爭不可或缺的專業(yè)伙伴。它從設(shè)備這一基礎(chǔ)要素著手,卻能在企業(yè)運營全局掀起效能革命,釋放出支撐高質(zhì)量發(fā)展的強大動能。
TPM咨詢重塑公司的設(shè)備管理體系?以上就是新益為TPM咨詢公司的相關(guān)介紹,做好企業(yè)的TPM咨詢工作就是為精益生產(chǎn)活動打下基礎(chǔ),讓精益生產(chǎn)管理在企業(yè)發(fā)展中有一個良好的發(fā)展前提。
文章來源于網(wǎng)絡(luò),版權(quán)歸作者所有,如有侵權(quán)請聯(lián)系刪除!
建立生產(chǎn)有序、管理順暢,操作規(guī)范,士氣高昂、高質(zhì)量、低成本、短交期的作業(yè)現(xiàn)場;
為企業(yè)規(guī)劃設(shè)計一套由內(nèi)到外的形象升級,外觀視覺價值體現(xiàn)、內(nèi)在的管理內(nèi)涵體現(xiàn);
全員參與設(shè)備管理高產(chǎn)出和低成本運營,提升設(shè)備管理能力,維護能力,提高效率
構(gòu)建班組生產(chǎn)管理體系、循環(huán)評價、人才育成、持續(xù)改善、績效管理、文化養(yǎng)成體系;
提高產(chǎn)品質(zhì)量、降低生產(chǎn)成本、縮短交期、增加利潤,讓管理更系統(tǒng)科學(xué),執(zhí)行力更強
對工廠的各個組成部分進行合理安排,以提高生產(chǎn)效率、降低成本、優(yōu)化物流、改善工作環(huán)境等